The Emergence of Digital Twins in Industry 4.0: A Deep Dive
The Emergence of Digital Twins in Industry 4.0: A Deep Dive
Table of Contents
- Understanding Digital Twins: Definition and Mechanics
- How Digital Twins Propel Industry 4.0 Forward
- Digital Twins in Manufacturing: Enhancing Efficiency and Precision
- Expanding the Scope: Digital Twins in Smart Cities
- Case Studies Highlighting the Impact of Digital Twins
- Conclusion: Embracing Digital Twins for a Smarter Future
Welcome to the advanced world of Industry 4.0, where digital twins are changing industries. This article explores what digital twins are, how they work, and their impact on different sectors. Whether you’re interested in technology or business, you’ll find useful insights and examples here that show how digital twins are making a difference. The concept of digital twins is not just a theoretical innovation but a practical tool that is reshaping how businesses approach design, maintenance, and operation across various domains. As we delve deeper, we’ll uncover the layers of technology and strategy that make digital twins a cornerstone of modern industry, illustrating their role through diverse case studies from healthcare to urban development.
Understanding Digital Twins: Definition and Mechanics
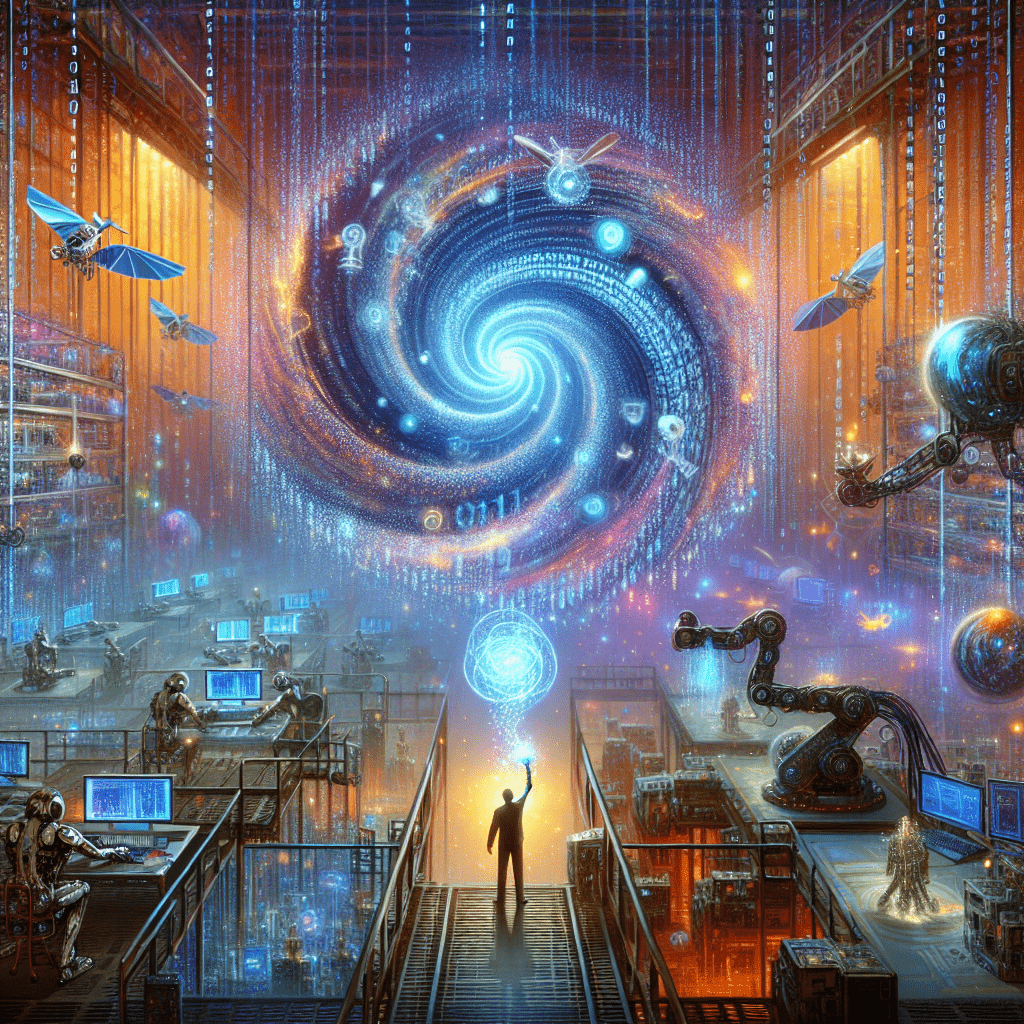
A digital twin is a digital version of a real object or system, made by collecting data from sensors on the real object. This virtual model updates in real-time as the real object changes. Digital twins are valuable because they provide immediate insights and future predictions, which are very important in today’s industry. The technology behind digital twins integrates IoT, AI, and machine learning to create dynamic systems that learn and adapt. These models serve as a bridge between physical assets and digital information systems, enabling a symbiotic relationship where data flows continuously, enhancing operational efficiency. The sophistication of these systems comes from their ability to not only replicate physical objects in a virtual platform but also to evolve based on new data, which provides a robust tool for decision-making and strategic planning.
- Real-time Monitoring: Constant data flow from real assets to their digital versions helps in making quick decisions. This capability allows industries to respond immediately to performance issues or environmental changes, ensuring minimal downtime and higher productivity. For example, in energy sectors, real-time monitoring through digital twins can detect anomalies in power grids or pipelines, prompting immediate preventative measures. This seamless integration of real-time data and predictive analytics helps industries like manufacturing and logistics maintain continuous operation and quality control, significantly reducing potential losses from unplanned outages or quality failures.
- Predictive Maintenance: By using past data and AI, digital twins can predict problems before they happen. This proactive approach reduces the need for reactive maintenance, which can be costly and disruptive. In aviation, digital twins of jet engines analyze data to forecast potential failures, scheduling maintenance before faults lead to cancellations or delays, thereby saving significant costs and enhancing safety. This approach is equally transformative in sectors like maritime and heavy machinery, where equipment downtime can have massive financial implications and risk to human safety.
- Simulation and Testing: Virtual scenarios allow for testing ideas and designs before making them real, saving resources and time. This process is especially valuable in industries like architecture and automotive, where the cost of physical prototypes can be exorbitant. By simulating different stress conditions and operational environments, companies can refine designs with greater accuracy, leading to better product quality and innovation. This capability extends to sectors such as aerospace and defense, where testing in a virtual environment can provide critical data without the risks associated with physical tests.
How Digital Twins Propel Industry 4.0 Forward
Digital twins are key to driving innovation and improving efficiency in Industry 4.0. A common mistake is to underestimate the planning needed for successful use. However, when used wisely, the benefits are significant. Effective integration of digital twins requires thorough understanding of both the technology and the business processes it aims to enhance. Organizations must cultivate a data-driven culture and invest in training to fully leverage the potential of digital twins. This strategic alignment between technology and business goals is crucial for maximizing the benefits of digital twins, from enhancing product lifecycle management to optimizing supply chain operations.
For example, in manufacturing, digital twins let managers test production methods in different scenarios to find the most efficient approach without real-world trials. This not only saves time but also cuts costs and improves product quality. A beverage company could use digital twins to simulate production lines under different conditions, such as changes in temperature or humidity, to optimize the consistency and quality of their products without halting actual production. This proactive testing and optimization lead to better resource management and can significantly boost profitability by minimizing waste and maximizing output.
Digital Twins in Manufacturing: Enhancing Efficiency and Precision
In manufacturing, digital twins help connect real operations with digital simulations, leading to big improvements in efficiency and productivity. For instance, a top carmaker uses digital twins to test car designs virtually before making them, which cuts down on time and costs related to physical prototypes and speeds up product launch. This integration of virtual and physical testing ensures that the final product meets quality standards and market expectations without the extensive use of resources typically involved in multiple rounds of physical testing. The rapid feedback loop enabled by digital twins allows for continuous improvement and agility in product development, crucial for staying competitive in today’s fast-paced market environments.
Expanding the Scope: Digital Twins in Smart Cities
Beyond manufacturing, digital twins are crucial in developing smart cities. These virtual models help city planners simulate traffic, disaster responses, and energy management, making cities safer and more efficient. Digital twins are powerful tools for sustainable city planning and managing city services and infrastructure. They enable planners to test the impact of various policies or infrastructure changes in a virtual environment before implementing them, reducing the risk and cost associated with urban development projects. This approach not only enhances urban resilience but also promotes more informed and democratic decision-making processes by providing a clear visualization of potential outcomes from proposed changes.
Case Studies Highlighting the Impact of Digital Twins
- Wind Farm Optimization: A European wind farm uses digital twins to improve turbine performance, greatly increasing energy production and lowering maintenance costs. By closely monitoring turbine conditions and environmental factors, the digital twin can suggest adjustments to operating parameters that optimize output and reduce wear and tear, leading to longer asset life and better ROI. This example illustrates how renewable energy sectors are leveraging digital twins to maximize efficiency and sustainability, a critical consideration in today’s environmentally conscious market.
- Hospital System Management: A U.S. hospital uses digital twins to better manage its facilities, improving patient care by optimizing surgery schedules and resource use. This system allows for better planning and allocation of medical staff and equipment, which in turn increases the hospital’s ability to handle higher patient volumes efficiently and with improved outcomes. The application of digital twins in healthcare extends to areas such as patient flow management and emergency response, enhancing the overall responsiveness and effectiveness of healthcare services.
- Supply Chain Management: A global logistics company uses digital twins to track and predict shipment statuses in real-time, enhancing delivery efficiency and customer satisfaction. This advanced tracking system integrates data from various sources, providing a holistic view of the entire supply chain, identifying bottlenecks, and suggesting alternative routes or methods to ensure timely delivery. The use of digital twins in logistics not only improves operational efficiency but also enhances transparency and accountability in supply chain management, crucial for building trust and reliability in global trade networks.
Conclusion: Embracing Digital Twins for a Smarter Future
Using digital twins in Industry 4.0 is crucial for staying ahead. They enhance manufacturing processes and revolutionize urban planning. These virtual models help us understand and manage complex systems better. If you want to keep up with technology, think about how digital twins can fit into your work or studies. The future is here, and it’s digitally twinned. As we continue to innovate, digital twins will play a pivotal role in making industries more adaptable, sustainable, and efficient.
Thank you for joining me on this exploration of **The Emergence of Digital Twins in Industry 4.0**. If you have questions or insights, feel free to share them below!